Product .. Wood Plastic Composites

Wood / plastic composites (commonly abbreviated as WPC) include those made by binding various recycled wood waste with recycled or virgin plastics . This combination can produce a variety of composite building products.
Recycled wood-based fiber and plastics could be used to produce a wide spectrum of products, ranging from inexpensive, low-performance composites to expensive, high-performance materials. Fiber technology, bonding performance, and fiber modification can be used to manufacture wood/plastic composites with uniform densities, durability in adverse environments, and high strength.
Wood-plastic composite is still a very new material relative to the long history of natural lumber as a building material but can be substituted in most instances. Besides being highly resistant to rot, the major advantage of this category of building materials is its ability to add another stage of upstream use to materials previously considered waste lumber.
A major advantage over wood is the ability of the material to be molded to meet almost any desired spatial conditions. It can also be bent and fixed to form strong arching curves. With up to 70 percent cellulose content (although 50/50 is more common), wood-plastic composites behave like wood and can be shaped using conventional woodworking tools. At the same time, they are moisture-resistant and resistant to rot . A major selling point of these materials is their lack of need for paint as they are manufactured in a variety of colors Filled thermoplastic composites are stiffer, stronger, and more dimensionally stable than their unfilled counterparts . Typical reinforcing fillers are inorganic materials like talc or fiberglass, but materials derived from waste wood, such as wood flour and recycled paper fiber, are also effective as fillers. Our goal is to generate commercial interest in using waste-wood-derived fillers (WWFs) to reinforce thermoplastics.
The manufacture of thermoplastic composites is often a two-step process : compounding or blending of the raw materials, and formation of the composite blends into a product.
Wood-Based Fibers
The waste wood flour identified for it's potential as reinforcing filler in thermoplastics. Wood flour is an economical, commercially available filler that has been used in thermoplastic composites to a limited extent.
Plastics
Polypropylene and high-density polyethylene (HDPE) were chosen as the matrix polymers. They are both widely used, are available at low cost, and have good performance for the intended applications. Their low melting points also allow processing below the degradation temperature of wood .
A wide variety of polypropylene and HDPE polymers are available, and careful selection is important because extrusion and injection molding require different material characteristics. For example, a critical need in injection molding is good flow of the material into the mold, whereas a critical need in extrusion is melt strength to enable handling of the hot material as it comes from the die. Choice of polymers for these technologies is therefore quite different. Injection molding requires a polymer with a low molecular weight to maintain low viscosity. By contrast, extrusion requires a polymer with a higher molecular weight for better melt strength.
Preparation and Feeding of Fillers
Conventional plastics equipment is designed to handle materials with a bulk density of approximately 500 kg/m3 . Although somewhat lower bulk densities can be handled, material with very low density is difficult to feed, requires specialized equipment, and can reduce processing rates. The wood flour is commercially available and has a bulk density of around 112-240 kg/m3 . Although lower in bulk density than thermoplastics, wood flour is sufficiently dense to be readily fed and dispersed ..


WPC Outdoor Decking & Fence

WPC Material Strength
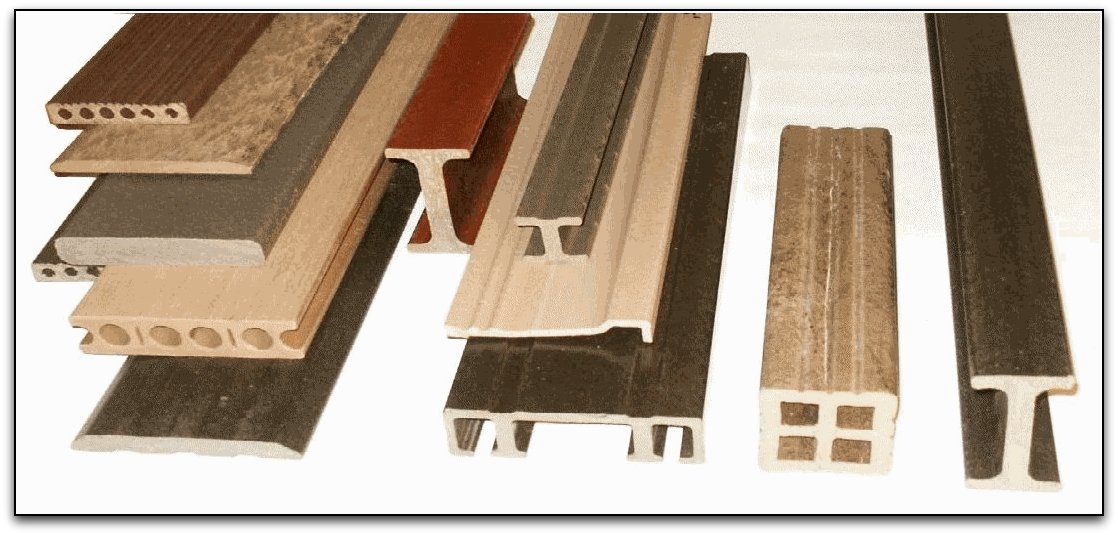
WPC Sections


WPC Doors ( Compound )

WPC Garden Bench
WPC Hollow Door







Recycled plastic sorting
First in Europe and now in the U.S., recyclers are coming to depend on SWIR-based spectroscopy for sorting plastics in the waste stream, as the images below illustrate. Cost effective SWIR 1024 or 512 element linescan cameras with wavelength sensitivities ranging from 1100 to 2200 nm are mounted onto a spectrograph. While monitoring the sorting conveyor, the spectrograph rapidly identifies the polymer type inherent in the waste and triggers the diversion of the waste into its proper bin.

Near infrared (NIR) spectroscopy identifies and sorts PE-HD, PE-LD, PP, PET, PET-G, PS, PVC, and similar plastics found in automotive, electronic, and household products. The plastics are first ground into little pellets and then sorted using a shortwave IR camera system. Of particular value is the ability of shortwave IR devices to sort black plastics; this detection and separation process is difficult to accomplish in the visible spectrum.
Color Separation for Plastic Recycling
(GmbH technology)
SPEKTRUM CS-P color separation systems identify and remove plastics of different colors. The material to be inspected is spread out on an external feeder and reaches the glass slide where the pieces are further individualized before continuing into the inspection area of the CCD linear camera which identifies their color .. Electronics evaluate the exact location of the components and ejection nozzles are activated with pinpoint accuracy and at precisely the right time to blow out the appropriate components into a vertical chute.
__________________________________________________________________________________
Copyright ©2016 Recycling Consult. All rights reserved